Cutting-edge technology in plastic extrusion for modern industries
Cutting-edge technology in plastic extrusion for modern industries
Blog Article
A Comprehensive Overview to the Refine and Advantages of Plastic Extrusion
In the vast realm of manufacturing, plastic extrusion arises as a very efficient and essential process. Transmuting raw plastic right into continuous accounts, it provides to a myriad of markets with its remarkable convenience. This guide aims to clarify the elaborate actions involved in this technique, the kinds of plastic appropriate for extrusion, and the game-changing advantages it brings to the market. The following discussion guarantees to unravel the real-world impacts of this transformative process.
Comprehending the Fundamentals of Plastic Extrusion
While it may appear complex at initial look, the procedure of plastic extrusion is basically straightforward. The procedure starts with the feeding of plastic material, in the form of pellets, powders, or granules, into a warmed barrel. The designed plastic is then cooled down, strengthened, and cut into wanted sizes, completing the process.
The Technical Refine of Plastic Extrusion Explained

Kinds of Plastic Suitable for Extrusion
The option of the right kind of plastic is an essential facet of the extrusion procedure. Different plastics offer one-of-a-kind properties, making them extra fit to certain applications. Recognizing these plastic types can dramatically improve the extrusion process.
Contrasting Plastic Extrusion to Other Plastic Forming Techniques
Recognizing the kinds of plastic suitable for extrusion leads the way for a more comprehensive discussion on just how plastic extrusion stacks up versus other plastic developing methods. These include shot molding, blow molding, and thermoforming. Each approach has its unique usages and advantages. Injection molding, as an example, is excellent for producing intricate components, while impact molding is ideal for hollow things like containers. Thermoforming excels at developing shallow or large components. Plastic extrusion is unrivaled when it comes to producing continual accounts, such as gaskets, seals, and pipelines. It also permits a regular cross-section along the size of the product. Therefore, the choice of approach largely depends on the end-product requirements and specifications.
Trick Advantages of Plastic Extrusion in Manufacturing
In the world of manufacturing, plastic extrusion uses many considerable advantages. One notable benefit is the cost-effectiveness of the procedure, that makes it an economically attractive manufacturing approach. Furthermore, this technique offers remarkable item adaptability and enhanced manufacturing speed, thereby enhancing total manufacturing efficiency.
Cost-efficient Manufacturing Technique
Plastic extrusion jumps to the forefront as an economical production approach in production. This process sticks out for its capability to create high volumes of material rapidly and effectively, supplying makers with considerable financial savings. The primary expense benefit is the capacity to make use of more economical resources. Extrusion uses polycarbonate materials, which are less expensive compared to metals or ceramics. Further, the extrusion process itself is reasonably basic, minimizing labor prices. In addition, plastic extrusion requires much less energy than standard production methods, contributing to lower operational prices. The process also minimizes waste, as any type of faulty or excess products can be reused and recycled, supplying one more layer of cost-effectiveness. Overall, the monetary benefits make plastic extrusion an extremely appealing option in the production industry.
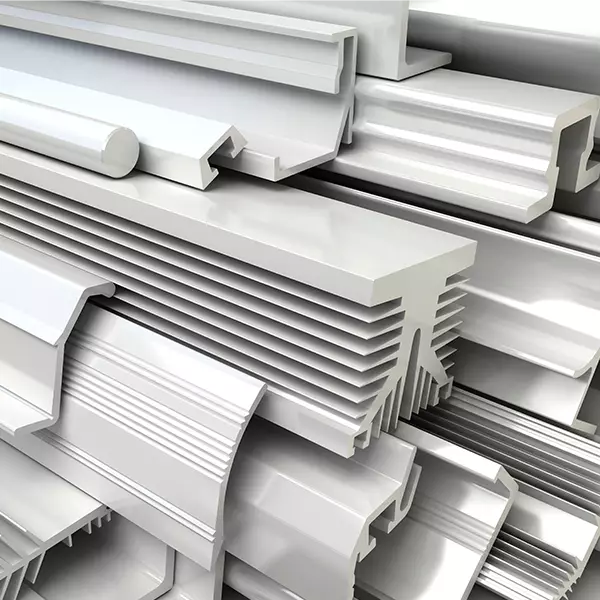
Superior Product Adaptability
Past the cost-effectiveness of plastic extrusion, one more considerable benefit in making depend on its remarkable product versatility. This process permits the creation of a wide range of products with differing dimensions, forms, and styles, from easy plastic sheets to intricate profiles. The adaptability is credited to the extrusion die, which can be tailored to produce the desired item style. useful link This makes plastic extrusion an optimal service for sectors that need customized plastic elements, such as automotive, building and construction, and packaging. The capacity to produce varied products is not just advantageous in conference particular market demands however also in making it possible for producers to discover new product with marginal capital expense. Fundamentally, plastic extrusion's item adaptability promotes technology while enhancing functional performance.
Enhanced Production Rate
A substantial benefit of plastic extrusion lies in its enhanced manufacturing rate. Few other manufacturing procedures can match the rate of plastic extrusion. Additionally, the ability to maintain regular high-speed production without giving up item quality establishes plastic extrusion apart from other approaches.
Real-world Applications and Impacts of Plastic Extrusion
In the realm of manufacturing, the technique of plastic extrusion holds extensive importance. This process is extensively utilized in the manufacturing of a address range of products, such as plastic tubes, window structures, and weather condition stripping. Because of this, it significantly affects industries like building and construction, packaging, and automotive markets. Furthermore, its impact includes everyday products, from plastic bags to tooth brushes and disposable flatware. The economic advantage of plastic extrusion, largely its high-volume and economical result, has changed production. The ecological influence of plastic waste stays an issue. The industry is constantly aiming for technologies in recyclable and biodegradable materials, suggesting a future where the advantages of plastic extrusion can be maintained without jeopardizing environmental sustainability.
Final thought
In conclusion, plastic extrusion is a extremely efficient and effective technique of changing raw materials right into diverse products. It uses countless benefits over various other plastic forming techniques, consisting of cost-effectiveness, high outcome, marginal waste, and layout versatility. Its impact is greatly really felt in different sectors such as construction, automobile, and customer items, making it a pivotal procedure in today's manufacturing landscape.
Delving much deeper right into the technological process of plastic extrusion, it begins with the selection of the proper plastic product. Once cooled down, the plastic is reduced into the required sizes or wound onto reels if the item is a plastic go to my site movie or sheet - plastic extrusion. Contrasting Plastic Extrusion to Various Other Plastic Forming Approaches
Recognizing the kinds of plastic ideal for extrusion leads the means for a wider discussion on how plastic extrusion piles up against other plastic developing techniques. Few various other production processes can match the rate of plastic extrusion.
Report this page